An overview of the slitter's functions: from basic operations to advanced cutting techniques
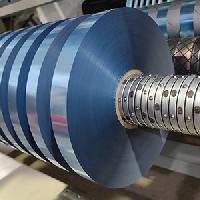
Posted by slittermachine
from the Business category at
21 Apr 2025 06:19:08 am.
1. Basic functions and operations
1. Material fixation and unwinding
◦ Unwinding system: automatic or manual feeding, equipped with an inflatable shaft or hydraulic chuck to hold the material rolls.
◦ Tension control: Constant tension unwinding is achieved through magnetic particle brake or servo motor to avoid material relaxation or breakage.
◦ Web Guiding Device (EPC): Automatically detects the position of the edge of the material to ensure that there is no misalignment during the slitting process.
2. Slitting method
◦ Round knife slitting: suitable for soft materials such as film and paper, and is divided into single knife (single point cutting) and multi-knife combination.
◦ Flat knife slitting: used for hard materials (such as metal foil) for a smoother cut.
◦ Extrusion slitting: Extrusion cutting by upper and lower knife rollers, suitable for elastic materials (such as non-woven fabrics).
3. Rewinding and splitting
◦ Independent winding reel: multi-spindle winding, multiple narrow reels can be produced at the same time.
◦ Surface winding/center winding: Contact or non-contact winding is selected according to the material characteristics.
◦ Automatic roll change: equipped with a material receiving mechanism to achieve non-stop roll change.
4. Basic parameter settings
◦ Slitting width, length, speed, tension, etc. are input through the human-machine interface (HMI).
◦ Supports manual fine-tuning (e.g., blade position, pressure).
Second, intermediate functions and technologies
1. High-precision cutting control
◦ Laser positioning system: real-time monitoring of cutting position, accuracy up to ±0.1mm.
◦ Dynamic tool pitch adjustment: Quickly switch between different slitting specifications through servo motor.
2. Expansion of material adaptability
◦ Multi-layer composite slitting: such as PET/AL/PE structure of food packaging film.
◦ Anti-stick treatment: For tape, release liner and other materials, avoid sticking during slitting.
3. Automated assistance features
◦ Automatic recycling of waste edges: Waste is collected by means of edge suction devices or winding systems.
◦ In-line quality inspection: Integrate cameras or sensors to detect defects such as burrs and cracks on the edge of slitting.
4. Data Recording and Traceability
◦ Store historical parameters (such as tension curve, velocity) and support production report export.
3. Advanced cutting technology
1. Intelligent slitting technology
◦ AI-optimized cutting path: Automatically calculates the optimal blade pressure and speed based on material properties.
◦ Adaptive Tension Control: Dynamically adjusts tension to cope with uneven material thickness (e.g., lithium battery pole pieces).
2. Special material handling
◦ Ultra-thin material (<10μm): fixed with a vacuum adsorption table to avoid wrinkles.
◦ High hardness materials (e.g. carbon fiber): Use diamond-coated blades or laser cutting heads.
3. Inline production integration
◦ Linkage with coating machine and printing machine: realize the fully automated assembly line of "unwinding-processing-slitting-winding".
◦ MES system docking: receive upstream process parameters and automatically match the slitting scheme.
4. Energy saving and loss reduction technology
◦ Low inertia slitting: Reduces material waste during start-stop.
◦ Ultrasonic slitting: No heat affected zone, suitable for sensitive materials such as medical films.
4. Safety and Maintenance
1. Security protection
◦ E-stop button, grating guard, blade guard.
◦ Overload protection (e.g. tension overrun alarm).
2. Maintenance points
◦ Lubricate the guide rails regularly and check the blade wear.
◦ Clean the sensor and guiding device.
5. Selection reference
Choose the type of slitter according to your needs:
• Economical: semi-automatic, suitable for low precision, small batches.
• High-end type: fully automatic + AI control, suitable for high value-added materials (such as optical film).
Once the functional hierarchy of the slitting machine is mastered, the user can gradually transition from basic operations to advanced technical applications, maximizing the value of the equipment and increasing the yield. In practice, the parameters need to be flexibly adjusted according to the material properties (ductility, thickness, viscosity, etc.).
Tags: slitting machine
0 Comments