Efficient and accurate: analysis of the core functions and applications of the slitting machine
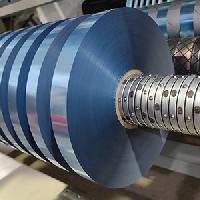
Posted by slittermachine
from the Business category at
21 Apr 2025 06:04:19 am.
First, the core function of the slitting machine
1. High-precision cutting
◦ Precision control: using servo motor or high-precision ball screw, the cutting accuracy can reach ±0.1mm or even higher, which is suitable for materials with strict size requirements (such as optical film, lithium battery separator).
◦ Dynamic guiding system: real-time monitoring of the edge position of the material through photoelectric sensor or CCD, and automatic adjustment of the position of the tool or coil to avoid deviation.
2. Efficient production
◦ High-speed slitting: Modern slitting machine speed can reach 1000m/min (such as paper, film slitting), with automatic tool change and winding technology, reduce downtime.
◦ Multi-axis synchronous control: Multi-station slitting can process multiple materials at the same time to improve efficiency (e.g., textile fiber slitting).
3. Intelligent operation
◦ Human-machine interface (HMI): touch screen control, preset parameters (width, tension, speed), support one-click switching specifications.
◦ Data traceability: Record production data (such as length, defects) for quality analysis and process optimization.
4. Material adaptability
◦ Multi-function knives: Round, flat or laser cutting heads can be configured to adapt to different materials (such as metal foils, composite materials, flexible circuit boards).
◦ Tension control: Closed-loop tension systems prevent material stretch deformation and are especially critical for elastic materials (e.g., rubber, nonwovens).
Second, typical application scenarios of slitting machines
1. Packaging industry
◦ Film slitting: Wide plastic film (PE/PP/PET) is cut into small rolls for food packaging and label substrates.
◦ Paper slitting: The slitting and rewinding of toilet paper and cardboard should ensure that the edges are flat and burr-free.
2. New energy field
◦ Lithium battery pole piece slitting: Copper foil/aluminum foil tab cutting, no burrs, no metal dust (to prevent the risk of short circuit).
◦ PV backsheet slitting: Precise slitting of PET substrate, width error affects module encapsulation.
3. Electronic materials
◦ FPC slitting: Laser slitting avoids mechanical stress damage to the circuit.
◦ Optical film slitting: The slitting of polarizers and brightness enhancement films should be in a clean environment to prevent scratches.
4. Textiles & Composites
◦ Carbon fiber prepreg slitting: High-precision control to avoid fiber splinter.
◦ Non-woven fabric slitting: rapid slitting of raw materials for medical masks, which needs to maintain the air permeability of the material.
3. Key technologies to achieve high efficiency and accuracy
1. Tooling system
◦ Diamond-coated tools: Longer life and less frequent replacement (suitable for hard materials such as ceramic sheets).
◦ Laser cutting: non-contact cutting, suitable for brittle materials (e.g., silicone, fiberglass).
2. Motion control technology
◦ Servo drive + encoder feedback: ensure that the tool position is synchronized to avoid accumulated errors.
◦ Floating winding mechanism: Adapts to the change of material thickness to prevent uneven winding.
3. Quality inspection integration
◦ In-line thickness gauge: real-time monitoring of material thickness and feedback adjustment (e.g., lithium battery separator).
◦ AI visual inspection: identify slitting edge defects (such as flashes and cracks) and automatically mark defective products.
Fourth, selection and optimization suggestions
• Material characteristics are preferred: Laser slitting machine is selected for hard materials, and tension control ability needs to be focused on elastic materials.
• Energy consumption ratio consideration: The high-speed slitting machine needs to be matched with energy-saving design (such as inverter motor, heat recovery).
• Modular design: easy to upgrade later (e.g. adding a dust collector or intelligent diagnostic module).
summary
The efficiency and precision of the slitter machine depends on the combination of mechanical precision, intelligent control and process adaptation. With the development of Industry 4.0, the slitter will further integrate the Internet of Things (remote monitoring) and AI optimization (predictive maintenance) in the future, becoming the core unit of flexible production. Enterprises should choose the matching technical solution according to their own material characteristics, capacity requirements and accuracy requirements when selecting models.
Tags: slitter machine
0 Comments