Micron slitting! How does the hot stamping foil slitting machine ensure that the edge is smooth and burr-free?
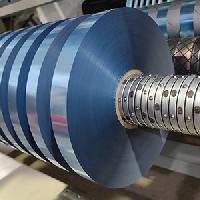
Posted by slittermachine
from the Business category at
18 Apr 2025 07:32:34 am.
1. High-precision slitting equipment
• Tooling system:
◦ Using diamond or cemented carbide tools, the cutting edge needs to be mirror polished (roughness ≤ 0.1μm), and the cutting edge angle is usually 20°~30° to ensure sharpness.
◦ Dynamically balance the tool spindle (speed error <0.001%) to avoid burrs caused by vibration.
• Tool setting system:
◦ Closed-loop control of servo motor + grating ruler, positioning accuracy needs to reach ±1μm, and repeated slitting error <±2μm.
◦ Air float or magnetic levitation guide reduces mechanical friction and ensures the smooth linear motion of the tool.
2. Tension control
• Multi-stage closed-loop tension control:
◦ The unwinding → the traction → winding adopts PID adjustment, and the tension fluctuation needs to be <0.5N (such as the Japanese Mitsubishi tension controller).
◦ The pretension is set to 5%~10% of the tensile strength of the material (e.g., PET foil is usually 2~5N/mm²).
• Web Guiding System:
◦ Photoelectric sensor + EPC correction, the accuracy is ±0.1mm, to prevent the material from misaligning and causing uneven trimming.
3. Optimization of process parameters
• Slitting speed:
◦ Adjust according to the thickness of the material: The slitting speed of 12μm gold foil is recommended to be 30~50m/min, and excessive speed can easily lead to heat accumulation burrs.
• Tool pressure:
◦ The pressure range is 0.2~0.8MPa (such as Japanese Komori slitting machine), which needs to be adjusted by real-time feedback of the pressure sensor.
• Temperature Control:
◦ Cutter head cooling system (20±1°C) prevents thermal deformation, and the ambient humidity is controlled at 45%~55% RH.
4. Material Handling
• Substrate pretreatment:
◦ The uniformity of the thickness of the aluminum plating layer needs to be <±3% (can be controlled by magnetron sputtering process).
◦ Balance material stress in a constant temperature and humidity environment (23±1°C) 24 hours before slitting.
• Release agent matching:
◦ The coating amount of silicone oil release agent is 1.2~1.5g/m² to avoid uneven coating peeling during slitting.
5. Quality inspection and feedback
• In-line inspection system:
◦ The laser profiler monitors the edge burr height in real time (threshold setting≤ 5 μm).
◦ Machine vision inspection system (2 μm resolution) to identify microscopic defects.
• Post-processing:
◦ Ionizing air knives to clean chips, or electrostatic adsorption to remove dust.
6. Maintenance and calibration
◦ Tool sharpening every 8 hours (Ra ≤ 0.05 μm) and forced tool change every 500 km slitting length.
◦ The laser interferometer calibrates the straightness of the equipment (error < 1 μm/m) weekly.
Through the combination of the above technologies, the burr height of hot stamping foil slitting machine can be controlled within 5μm, which can meet the process requirements of high-end packaging (such as cigarette labels and luxury goods). In actual production, the parameters need to be dynamically adjusted according to the material batch, and it is recommended to determine the optimal process window through DOE (Design of Experiments).
0 Comments