Lean Six Sigma Green Belt Certification for Businesses
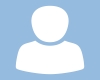
Posted by Mark
from the General category at
08 Dec 2023 12:18:46 pm.
Keeping a business at a constant level of productivity and reducing unwanted errors that affect profit are two essential aspects that every manager wants to learn. Being consistent is not easy since the market is continuously changing, and so are the demands and needs of customers. Company owners are always looking for intelligent and efficient ways of correcting their manufacturing errors to maintain the performance of their processes.
To come to their assistance, various methodologies have been developed and gradually improved so that variation can be eliminated and the result will be satisfactory both for the manager and the client. Six Sigma and Lean management are two techniques that have shown excellent results whenever they were implemented into a process. Given the success rate of the two methodologies, they were merged into a more complex technique that can be generally applied in several industries. In the following lines, we will present and explain the particularities of the Lean Six Sigma green belt and how it can help you grow your business into a strong and profitable one.
Lean Six Sigma Green Belt: a Perfect Combination
Six Sigma is organized and divided into various categories, each named after a belt typically used in martial arts. The Green Belt is the third and most popular level, being the easiest to apply and with the most successful results. Each certification is available for managers and employees to obtain to help them enhance their knowledge and master the fundamental principles of this approach. Six Sigma includes the following certifications:
- Six Sigma White Belt contains an introductory level into the concepts of Six Sigma.
- Six Sigma Yellow Belt proves that you have learned the particularities of the methodology and how they can be applied to your business or workplace.
- Six Sigma Green Belt includes a deep analysis of the problems and provides solutions for correcting them. It’s the first stage at which the applicant can develop strategies that improve projects.
- Six Sigma Black Belt states that you are an expert in the principles of Six Sigma and can take on more serious tasks inside an organization.
- Six Sigma Master Black Belt is the top level at which the applicant has obtained intensive knowledge and can occupy leading positions inside a company.
Lean Six Sigma Green Belt is all the more effective as it combines the particularities of both techniques, eliminating all the unnecessary things that create errors and don’t add value to the final product or service. The methodology focuses on increasing efficiency by reducing waste, the central aspect that negatively influences profit. The term refers to the deviation curve, suggesting that errors in any process have 3.4 defects per million opportunities. The Green Belt level enables managers to find targeted solutions to their quality-related problems, thus correcting errors that affect the final state of the product or service delivered. Green Belts can also analyze and review solutions provided by lower-grade belts since they are more experienced and have gained a better knowledge of the methodology.
Often, applicants who achieved the Lean Six Sigma Green Belt certification can lead their projects, occupying higher functions inside a company. The accreditation allows them to apply the tools learned during the course, including measuring, analyzing, defining, controlling, and improving regular problems that might occur during the daily manufacturing processes.
Obtaining the certification brings financial benefits, as the Green Belt owners are wanted by managers looking for team leaders and managers for various company sectors. Hiring managers put a great price on these credentials and look for experienced candidates for high-level jobs. Hence, employees who prove to have knowledge and expertise in implementing Lean Six Sigma Green Belt principles can occupy high positions and enjoy more significant salaries.
Particularities of Lean Management
Toyota was the first company to ever design and implement the methodology in their attempt to minimize waste and correct the errors that affect productivity in any way. Its main goal is to reduce the amount of resources put into developing a product or service for higher profit without affecting its quality.
The first step is to detect what is creating waste, or what is slowing down or hardening the process, any non-value task that either increases the manufacturing costs and time or impacts the quality. Lean principles state that working in a positive environment directly influences the final product because satisfied employees yield better. The overall improvement is visible in customer feedback but also in employee satisfaction.
The 5 Main Principles of Lean Management
The whole methodology was developed around five core ideologies, which guarantee success in achieving constancy and eliminating adverse effects.
1. Identify Value
The first step is to identify the value you want your company to achieve and strive to add that value to the product that reaches the customer. This way, you will manage to deliver a product that the customer will pay for. To achieve the said value, you need to use resources that increase the quality without increasing the costs; otherwise, you will create waste.
2. Create a Map of the Value Chain
Next, you must create the workflow map, more precisely, make an inventory of all the steps and the people involved in creating the product from start to finish. This way, you will identify what is necessary and what can be eliminated to add value to the product delivered to the customer.
3. Create a Continuous Workflow
After creating the map, you will be able to determine the role of each team in the manufacturing process. It’s essential to have all your departments working together to ensure a smooth workflow. To minimize interruptions and bottlenecks, divide the tasks into smaller portions so the team can finalize them.
4. Implement a Traction System
The fourth principle implies that work should only be done if there is a demand. A company should never work in advance, as this might waste precious resources that should only be used when the need is real. Teams that work unnecessarily will not yield as expected.
5. Pursue Continuous Improvement
Once you have implemented the previous principles, all that remains is to maintain continuous improvement to avoid letting all your efforts go to waste. As the manufacturing process keeps changing and is constantly influenced by various external factors, you need to ensure your team will do their best to maintain the improvement level you achieved.
0 Comments