What are the various types of processing equipment and technologies that are utilized for precision
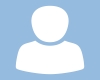
Posted by white
from the Technology category at
20 Jun 2023 12:53:10 am.
The Electrical Discharge Machining (EDM) process is well-suited for the manufacturing of complex parts with features such as precision small cavities, narrow slots, grooves, corners, and so on. This process was developed in the 1950s. EDM is utilized in circumstances in which it is difficult for the tool to reach the complex surface, circumstances aluminum die castings in which it is necessary to perform deep cutting, and circumstances in which the aspect ratio is particularly high. In comparison to milling, this method is a significant advancement. Recharging the milling electrodes used in the production of high-tech components can contribute to an increase in the percentage of successful attempts made. Machining with electric discharge is recommended over other machining methods due to the lower tool costs associated with it. Other machining methods can have quite high tool costs. In addition, EDM can be utilized to provide a surface with a fire pattern in circumstances where it is specified that EDM finishing is required. This is the case when the EDM finishing requirement is specified. The surface of parts, particularly workpieces that have been hardened, can be finished with the help of grinding machines, which are pieces of precision equipment that are used to finish the surface. Surface grinders, universal internal and external cylindrical grinders, coordinate grinders (PG optical curve grinders), and universal cylindrical grinders are the most common types of grinding machines used in mold processing. Other types of grinding machines include universal internal and external cylindrical grinders.
The primary application for the technique of slow wire cutting is the processing of two-dimensional and three-dimensional ruled surface parts. These parts include a wide variety of dies, plastic molds, and powder metallurgy molds. When it comes to the processing of a large number of precision holes, such as those found in punches, punch fixing plates, dies, and stripping plates of stamping dies, slow wire cutting processing is an important and necessary key technology that must be utilized. A significant portion of these processes is devoted to the preparation of stamping dies. A few examples of common applications that are utilized in the production of injection molds include insert holes, ejector pin holes, inclined ejector holes, cavity cleaning angles, and sliders. When compared to the requirements for stamping molds, the requirements for processing accuracy are typically less stringent. The use of the slow wire processing method allows for an extremely high level of precision to be accomplished. It is possible for high-end machine tools to achieve a processing accuracy of less than 3 micrometers and a surface roughness of less than 0. 05 micrometers. At the moment, it is feasible to perform automatic wire threading cutting on electrode wire measuring 0. 02-0. 03mm, and the cutting efficiency, when put into practice, is able to reach approximately 200mm2/min.
CNC lathes continue to advance in terms of both the machining accuracy and the manufacturing technology that they possess. As a consequence of these advancements, there is a growing tendency to use lathes rather than grinding machines. In addition to their widespread use in pen molds and bottle mouth molds, they are frequently applied in the processing of circular inserts, support heads, positioning rings, and various other components of molds. Their applications range from simple to highly complex. In point of fact, the capabilities of modern CNC lathes have progressed to the point where they are now turn-milling machine tools in addition to their traditional turning capabilities. This is due to the fact that modern CNC lathes have undergone this evolution. Even a complicated component that calls for a number of different processes can have everything completed simultaneously. When digital surveying and mapping are carried out in the early stages of mold design, high-precision measurement equipment plays an important role in both of these processes. In the later stages of mold design, this equipment also plays an important role in the measurement of the mold processing process, the measurement of mold acceptance, and the measurement of mold repair.
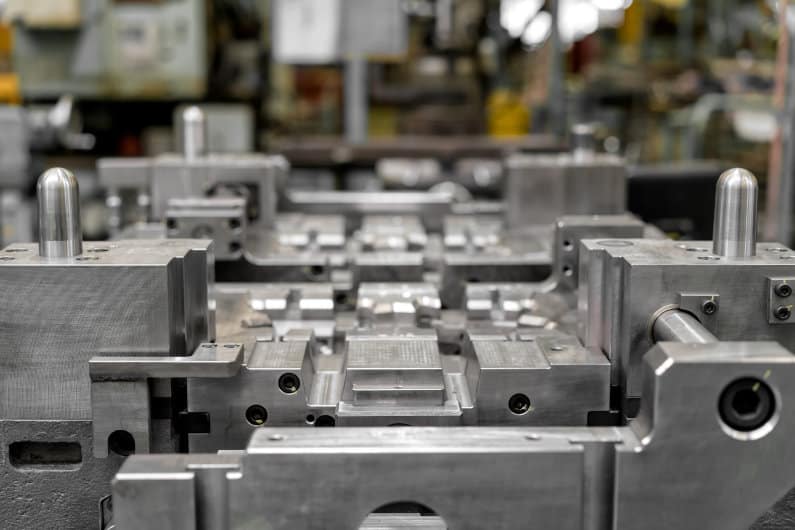
The primary purpose of the Xiaoping grinder is to process mold components of a small size. These components include precision inserts, precision mold cores, sliders, and other components that are functionally analogous. When processing larger-sized templates, it is frequently necessary to make use of larger water grinders. It is now common practice to use a surface grinder that has a high-speed table movement and to increase the speed at which the grinding wheel line moves. Increasing the speed at which the grinding wheel line moves also speeds up the process. The implementation of cutting-edge technologies for functional components has directly die casting services led to a significant increase in the rate of movement. These cutting-edge technologies include, amongst other things, linear guide rails, linear motors, and static pressure screw screws. In addition, the grinding wheel has been the subject of steady improvement over the course of its history. Trimming technique. CNC lathes are another piece of processing equipment that is frequently utilized in mold workshop settings. These machines are capable of processing a wide variety of rotary parts, so their application is widespread. Because of the rapid development of numerical control technology, it is now possible to easily realize complex shapes of rotary bodies by making use of programming. This was not possible in the past. In addition, machine tools now have the capability to change tools automatically, which significantly boosts the efficiency of the production process.
Automated system for quick clamping and positioning, in addition to other functionsThere is typically more than one process that needs to be completed before a mold part can be successfully manufactured. It takes a significant amount of time because the components have to be continuously clamped and corrected throughout this process. In addition to this, the machine tool is in a state of idleness during this time, and the processing capacity of the costly equipment is not being utilized to the full potential that it possesses. The manufacturing industry is moving in the direction of shorter production cycles as a general development trend. This pattern is being propelled forward by the fiercer and fiercer competition that can be found in the manufacturing sector. Because foreign fixture manufacturers use a set of reliable and accurate reference systems to realize the unified reference exchange of milling, turning, measuring, EDM, and other processes, it only takes about a minute to quickly complete clamping and processing of electrodes on the machine tool. This is possible in such a short amount of time because of the foreign fixture manufacturers. This makes it possible for the manufacturers of foreign fixtures to participate in the unified reference exchange. Within three micrometers, the accuracy of alignment and repeat positioning allows for a significant reduction in the amount of time spent setting up the machine tool and a significant improvement in the amount of time it spends actually operating. It has been demonstrated that fulfillment of this requirement is necessary for the production of modern goods.
Tags: aluminum die castings
0 Comments